Reaktive Instandhaltung
Was versteht man unter “Reaktiver Instandhaltung”?
Reaktive Instandhaltung ist eine Instandhaltungsstrategie, bei der Wartungs- und Reparaturarbeiten durchgeführt werden, nachdem ein Problem oder ein Ausfall bereits aufgetreten ist. Diese Methode basiert auf dem Prinzip des “Reparierens nach Bedarf” und wird oft ohne vorherige Planung oder regelmäßige Wartungsintervalle durchgeführt.
Unterschied zur “Ausfallbedingten Instandhaltung”
Reaktive Instandhaltung und ausfallbedingte Instandhaltung unterscheiden sich hauptsächlich im Umfang und Fokus ihrer Anwendung. Reaktive Instandhaltung umfasst ein breiteres Spektrum an Problemen und bezieht sich auf die Durchführung von Wartungs- und Reparaturarbeiten, sobald ein Problem oder eine Störung auftritt. Dies kann sowohl kleinere Störungen als auch komplette Ausfälle umfassen, ohne vorherige Planung oder regelmäßige Wartungsintervalle.
Im Gegensatz dazu konzentriert sich ausfallbedingte Instandhaltung spezifisch auf die Behebung von vollständigen Ausfällen oder Betriebsunterbrechungen. Diese Art der Instandhaltung wird durchgeführt, wenn eine Maschine oder Anlage nicht mehr funktioniert und vollständig ausgefallen ist. Während die reaktive Instandhaltung darauf abzielt, jegliche auftretenden Probleme zu beheben und den Betrieb so schnell wie möglich wiederherzustellen, liegt der Schwerpunkt der ausfallbedingten Instandhaltung ausschließlich auf schwerwiegenden Störungen, die den gesamten Betrieb beeinträchtigen.
Ziele und Vorteile der reaktiven Instandhaltung:
- Minimale Planungsanforderungen: Da Wartungsmaßnahmen erst nach einem Ausfall erfolgen, ist keine umfangreiche Vorausplanung erforderlich.
- Volle Nutzung der Lebensdauer: Maschinen und Anlagen werden bis zu ihrem tatsächlichen Ausfall genutzt, was eine maximale Nutzung der investierten Ressourcen ermöglicht.
- Einfache Umsetzung: Diese Methode erfordert weniger organisatorischen Aufwand und Ressourcen, da Wartungen nur bei Bedarf durchgeführt werden.
Nachteile:
- Ungeplante Ausfallzeiten: Da die Instandhaltung erst nach einem Ausfall erfolgt, können unerwartete Produktionsunterbrechungen auftreten, die zu erheblichen Kosten und Verzögerungen führen.
- Höhere Reparaturkosten: Reparaturen nach einem Ausfall können teurer sein als präventive Wartungsmaßnahmen, insbesondere wenn der Schaden umfangreich ist.
- Sicherheitsrisiken: Ausfälle können zu gefährlichen Situationen führen, insbesondere bei sicherheitskritischen Maschinen und Anlagen.
Typische Maßnahmen:
- Fehlerdiagnose: Identifikation und Analyse der Ursache des Ausfalls, um die erforderlichen Reparaturen durchführen zu können.
- Reparatur und Austausch: Austausch defekter Teile oder Reparatur beschädigter Komponenten, um die betroffene Maschine oder Anlage wieder funktionsfähig zu machen.
- Wiederinbetriebnahme: Nach der Reparatur wird die Maschine oder Anlage getestet und wieder in Betrieb genommen, um sicherzustellen, dass sie ordnungsgemäß funktioniert.
Implementierung:
Die reaktive Instandhaltung erfordert eine schnelle Reaktionsfähigkeit und eine effiziente Organisation. Wichtige Schritte umfassen:
- Bereitstellung von Ersatzteilen: Sicherstellung, dass wichtige Ersatzteile verfügbar sind, um die Ausfallzeit zu minimieren.
- Schulung des Personals: Das Wartungspersonal muss in der Lage sein, schnell und effektiv auf Ausfälle zu reagieren und Reparaturen durchzuführen.
- Dokumentation: Protokollierung aller aufgetretenen Störungen und durchgeführten Reparaturen, um Daten für eine zukünftige Optimierung der Instandhaltungsstrategie zu sammeln.
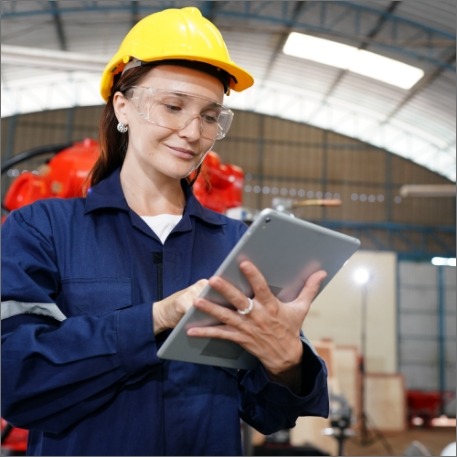
Kostenloser Quick-Check Ihrer Anlagenkennzeichnung:
Mit unserem Quick-Check helfen wir Ihnen, in nur 5 Minuten ein erstes Bild zu erhalten. Kostenfrei & unverbindlich.