Wear, defect, failure: the importance of maintenance
Maintenance is of great importance in industry. The Menger Group explains why it is so important for companies.
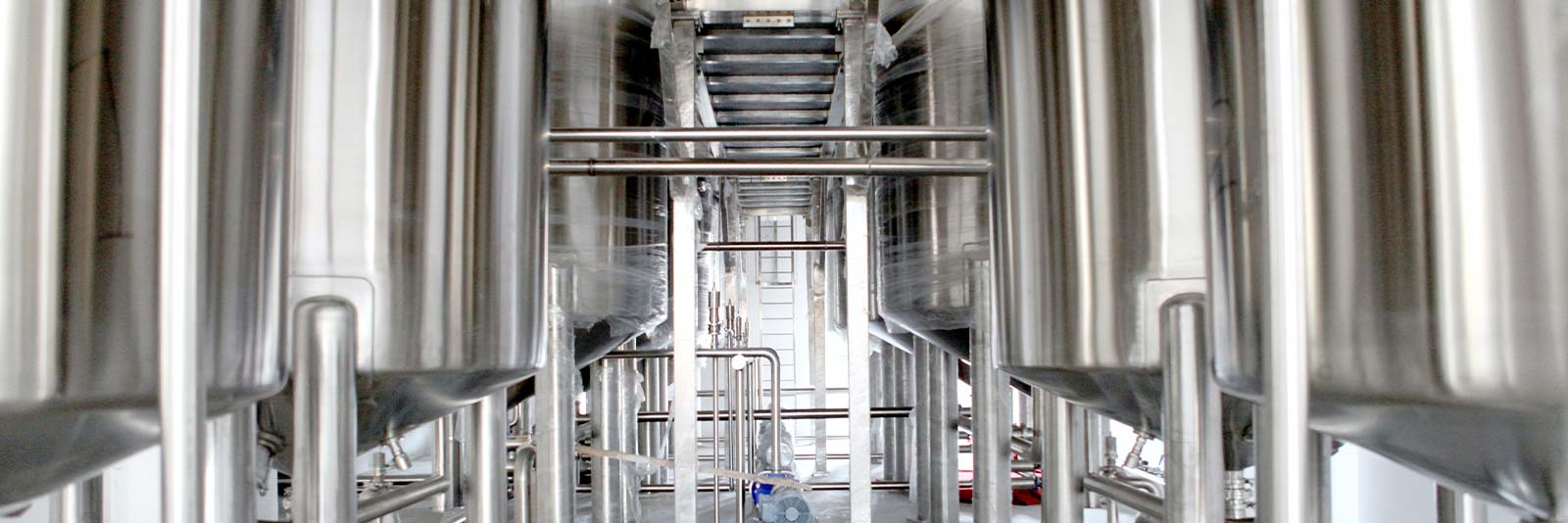
So that machines and plants run smoothly for a long time
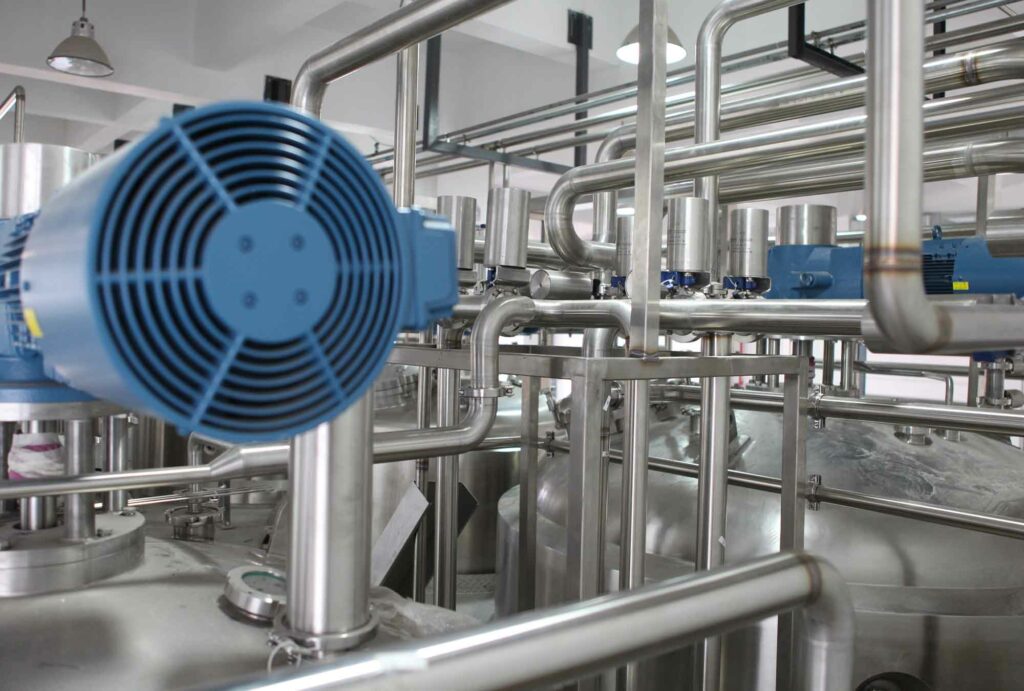
The proper functioning of machinery and equipment is the backbone of many businesses. To keep everything running smoothly, their maintenance is of great importance. Maintenance serves to extend the service life of machinery and equipment and to minimize downtime and costs. To this end, maintenance includes the administrative and technical measures of inspection, maintenance, repair and improvement. These measures to ensure the target condition of a machine or plant and the exact meaning of the frequently synonymously used terms are explained to you by the Menger Group.
What is understood by maintenance?
Maintenance is the generic term for all measures that are intended to ensure the smooth functioning of machines and systems. This means, on the one hand, maintaining functionality and, on the other hand, restoring it in the event of a malfunction. These measures include inspection (including weak-point analysis), maintenance, repair and improvement.
In the definition of DIN 31051, it sounds like this: “Maintenance is the combination of all technical and administrative measures as well as management measures during the life cycle of a unit of consideration to determine and assess the actual condition and to maintain the functional condition or return it to this condition so that it can fulfill the required function.” In simple terms, then, the importance of maintenance is to assess the actual condition of a machine or system and to maintain or, if necessary, restore it to its desired condition.
Maintenance includes preventive, corrective and “predictive” measures. Preventive maintenance includes all measures that are carried out as part of condition-based or predefined maintenance. Corrective maintenance includes all work that is initiated after a malfunction has occurred. Predictive maintenance, which is still in its infancy, is based on extensive data analysis and information on the expected wear and tear of an object. Its importance for maintenance will continue to grow in the future.
What tasks are part of maintenance?

According to DIN 31051, the following basic measures belong to maintenance: inspection, servicing, repair and improvement.
Inspection
Within the scope of maintenance, the inspection serves to regularly determine the actual condition of a machine or system. For this purpose, a qualified person carries out a function check, checks measured values and checks system parts and settings. The actual condition of the object is determined and documented. The checks include, among other things:
- Checking of settings, measured values, filling levels
- Checking for signs of wear on components and operating equipment
- Visual inspections of wear parts, wear measurements
- Corrosion tests
- Assessment of wear
- Investigation of the reasons for wear (normal wear or defect?)
By comparing the inspection results with the target condition, the inspector finds out whether the machine is working properly and safely. The result of the inspection decides on the further procedure and thus has a groundbreaking significance for maintenance.
Maintenance
Maintenance is a measure to maintain the target condition. It involves minor work on the equipment that delays or prevents wear. In the process, it thus ensures an operational extension of the service life of the plant. Therefore, maintenance is of great importance for the overall maintenance. The maintenance works include:
- Cleaning and maintenance
- Lubrication of plant components
- Carrying out a test run
All work performed should be logged, because the log serves as proof when it comes to warranty claims or the resale of a plant. How often maintenance is necessary depends on numerous different factors. The maintenance interval should therefore be determined individually for each object or system.
Repair
Reconditioning serves to restore the target condition if, for example, a malfunction or damage was detected during the inspection. This can be, for example, the repair or replacement of a component. Reasons for a malfunction can be:
- Wear due to wear or material fatigue
- friction or corrosion
- poor maintenance or incorrect use
- an accident or exposure to force
After the repair, both the function and the safety of the system must be restored in the sense of the target condition. All work carried out as part of the repair should also be recorded by the plant operator.
Improvement
An improvement ultimately serves to optimize the functional safety of a machine or plant without, however, changing the actual function of the object. According to DIN 13051, “functional safety” is a collective term for availability, reliability, maintainability and maintenance capability of the object. The objectives of an improvement include:
- a modernization
- an improvement of the utilization potential
- an increase in efficiency
of the machine or system under consideration. This reduces the maintenance and servicing effort in the medium to long term, which in turn reduces the costs of maintenance. An important tool for improvement is the weak point analysis, which is used to determine the optimization potential of the object.
The competent execution and documentation of maintenance measures requires some know-how. However, since the importance of maintenance is essential for most companies, the Menger Group offers you reliable and competent support in all related matters. Whether service, method or software – contact us!