Maintenance of the future
In the future, the maintenance of machines and plants will be increasingly characterized by automation. The Menger Group presents some important development.
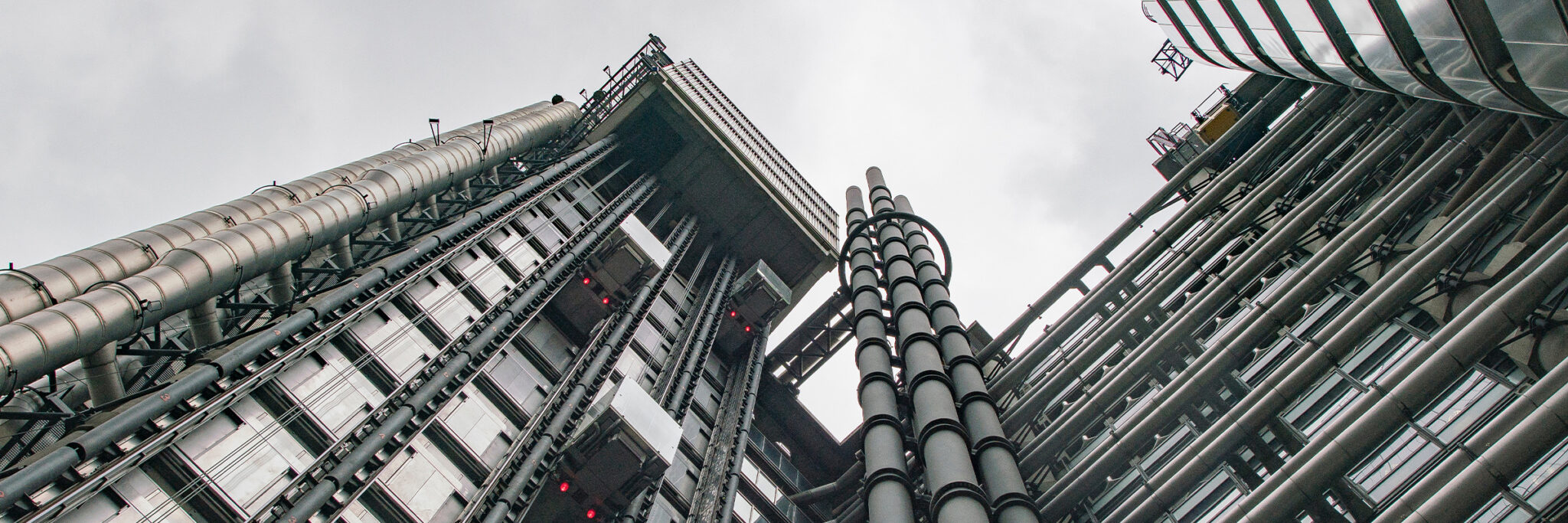
How digitization and outsourcing are changing maintenance
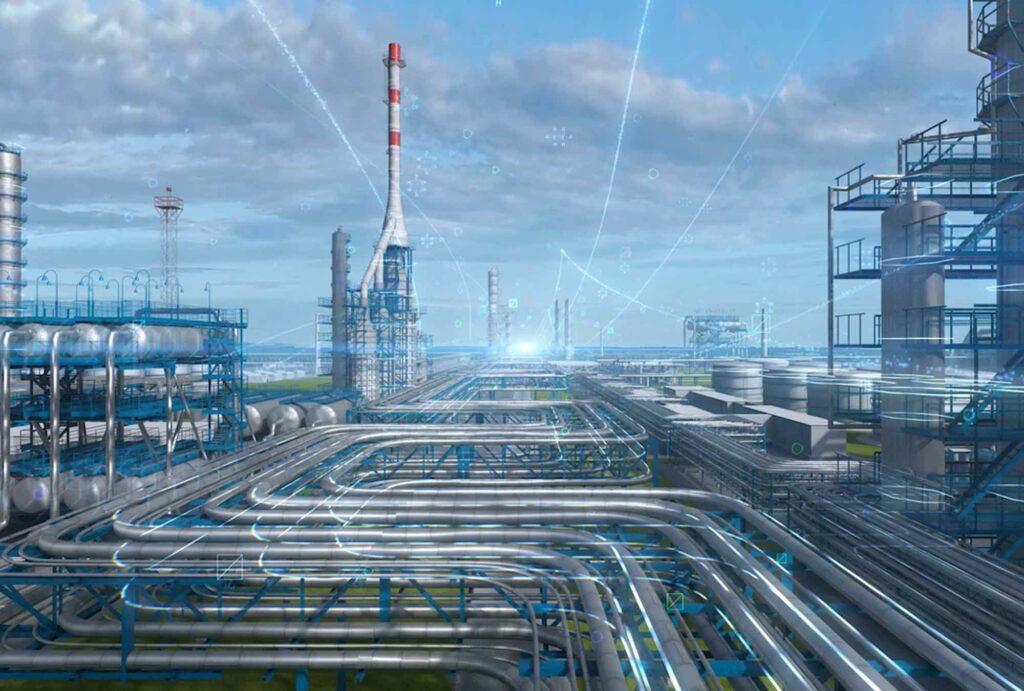
Based on current trends, it is already possible to foresee what the maintenance of the future could look like: It will be characterized by automation, digitization and artificial intelligence. At the same time, services will increasingly be provided by specialized companies. The Menger Group presents the most important trends in the field of maintenance, looks at the opportunities and challenges of change, and ventures an outlook on how maintenance will be carried out in the future.
Trends and changes in the field of maintenance
Maintenance includes all work on a machine or system that serves to maintain or restore its target condition. Up to now, two types of maintenance have been the most common:
- Corrective maintenance, which takes place after damage has occurred and is designed to repair it and restore the original functionality of the machine or equipment.
- Preventive maintenance, which takes place at regular intervals and includes specified maintenance measures such as the replacement of wear parts.
Carefully performed preventive maintenance in particular makes it possible to avoid unforeseen failures due to damage or malfunctions. However, it also has a major disadvantage: As a rule, maintenance intervals are fixed. This often results in the replacement of components of systems that are still fully functional. However, if the maintenance interval of the machine were simply extended in response to this realization, then this would increase the risk of undetected damage and thus sudden failures.
Trends and changes in the field of maintenance
Companies that want to increase their efficiency and hold their own in the market cannot avoid optimizing their maintenance in the long term. This is the only way to minimize the risk of machine and plant failures and unplanned downtime. At the same time, modern machines are so technically complex that their maintenance is also becoming increasingly demanding.
The maintenance of the future will face this in various ways. The most important features include the growing importance of digitization and the use of artificial intelligence, which makes it possible to evaluate large volumes of data automatically. For example, in line with the principle of predictive maintenance, it will be possible to carry out certain maintenance work precisely when it is necessary – for example, by sensors continuously determining measurement data on the condition of a machine and triggering the necessary maintenance measures in the event of a significant deviation from the defined standard value. The networking of man and machine, the goal of Industry 4.0, will thus also play an ever greater role in the optimization of maintenance and will become very important in the future.
Another contribution of digitization to improving maintenance is the preservation and transfer of knowledge. Whenever a plant maintenance employee retires, he takes valuable knowledge about machines and plants with him. Part of this knowledge is in the documented plant history and can be made transparent and accessible through digitization. This is where the maintenance of the future overlaps with the large topic area of document management, especially also with regard to electronically available work instructions and notes on the special features of certain machines. In the case of routine tasks that can be automated, as well as predictive maintenance using artificial intelligence, on the other hand, outsourcing of maintenance will gain in importance in the future. Certain trends already indicate such developments in maintenance today.
Condition-Based Maintenance
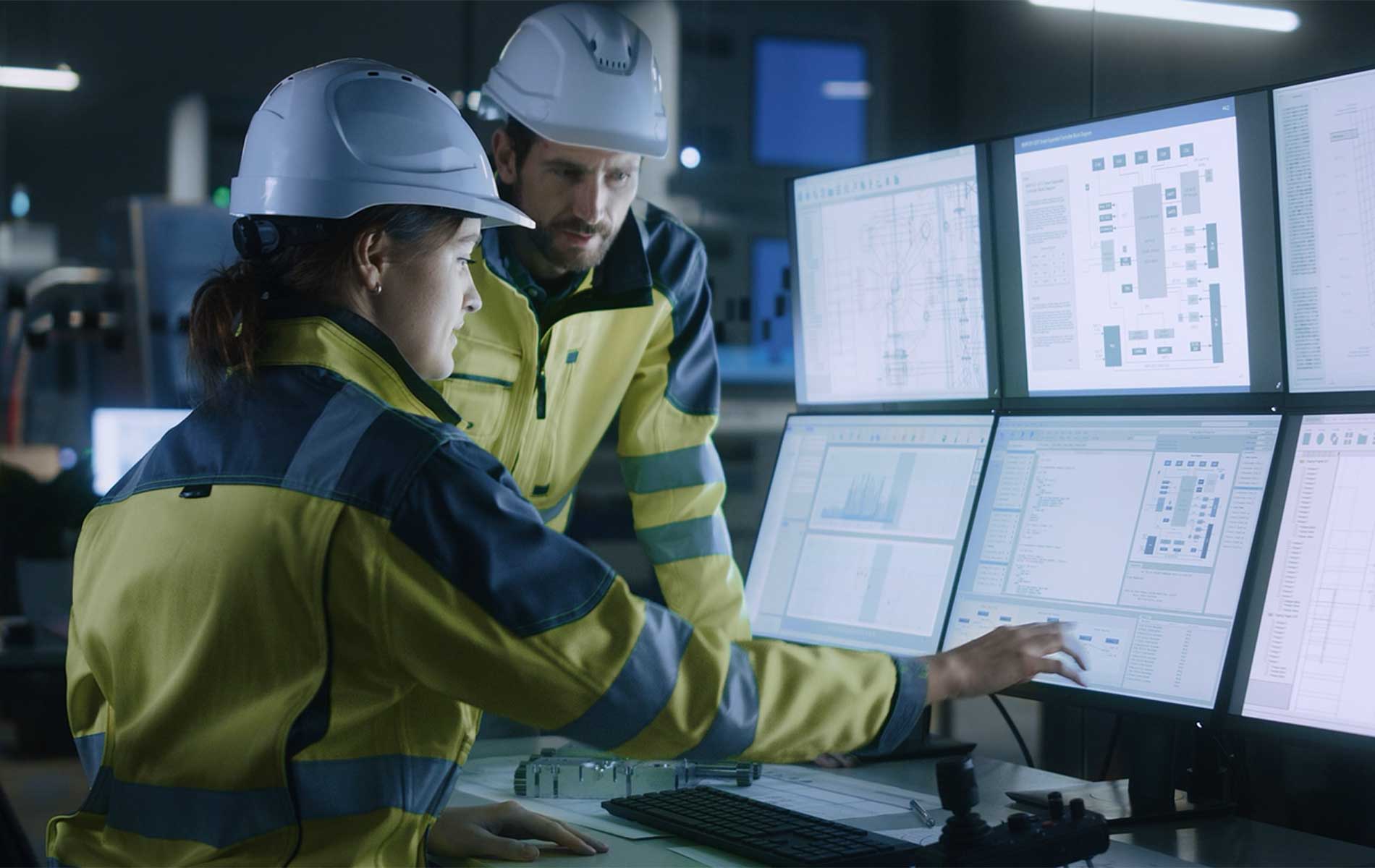
Condition-based maintenance is based on constant monitoring of the actual condition of machines and systems, either through regular inspections or with the aid of integrated sensors. The latter constantly record measured values, such as pressure or temperature during a work process, and forward them for evaluation. The recipient of the data can be, for example, the manufacturer of the machine or an external service provider.
If the evaluation reveals that certain measured values are outside a specified standard range, this automatically triggers the instruction for a corresponding maintenance measure – for example, the immediate replacement of a component or even the note that it should be replaced at the next scheduled shutdown. Malfunctions or damage can thus be detected and repaired at an early stage, even before they cause any disruption to work processes.
Predictive Maintenance
The actual predictive maintenance takes this principle further. Here, the manufacturer of a machine collects as much data as possible about its functionality and any damage that occurs. This data forms the basis for later making predictions, with the help of artificial intelligence, about when and under what circumstances damage will occur to a machine of this type. To this end, the artificial intelligence is trained with the available data so that it is later able to evaluate information on the actual condition of such machines with regard to possible damage.
The greater the number of available data sets and the higher their quality, the more accurate the predictions that can be made. Therefore, this type of predictive maintenance requires that companies are willing to share data with the manufacturer about their machines and, if possible, about the conditions under which they are used.
Maintenance outsourcing
Another major trend in maintenance is the outsourcing of both routine tasks and those associated with particularly high IT requirements. Routine tasks, for example the regular maintenance of machines, can often be automated – the automatic measurement and evaluation of condition data is one example. Very specialized tasks, on the other hand, such as the evaluation of large volumes of data described above and the prediction of damage and faults based on this, require a high-performance IT infrastructure. This can often be provided by external service providers more easily and at lower cost than would be possible for the company’s own maintenance department.
Nevertheless, in-house maintenance will continue to play an important role in the future. This is because the company’s own employees are on the spot immediately in the event of problems, know exactly the characteristics of the machines and are aware if measured values deviate from the normal state due to unusual requirements or events. In the future, targeted cooperation between operational and external maintenance will extend the service life of machines and systems, reduce maintenance costs and improve the efficiency of the company.
Optimized maintenance increases the efficiency of your company
Of course, optimizing maintenance in a company does not happen overnight. Rather, it is initially a medium- to long-term process. This is associated with high initial investments, which are, however, more than offset by increases in efficiency. By detecting and repairing damage at an early stage, even before malfunctions or even breakdowns of the affected machines occur, the maintenance costs are permanently reduced and the productivity of the entire company is increased at the same time.
The Menger Group will be happy to assist you at any time with the professional optimization of maintenance in your company. From special software solutions to services, we are your partner for all aspects of maintenance and maintenance management.
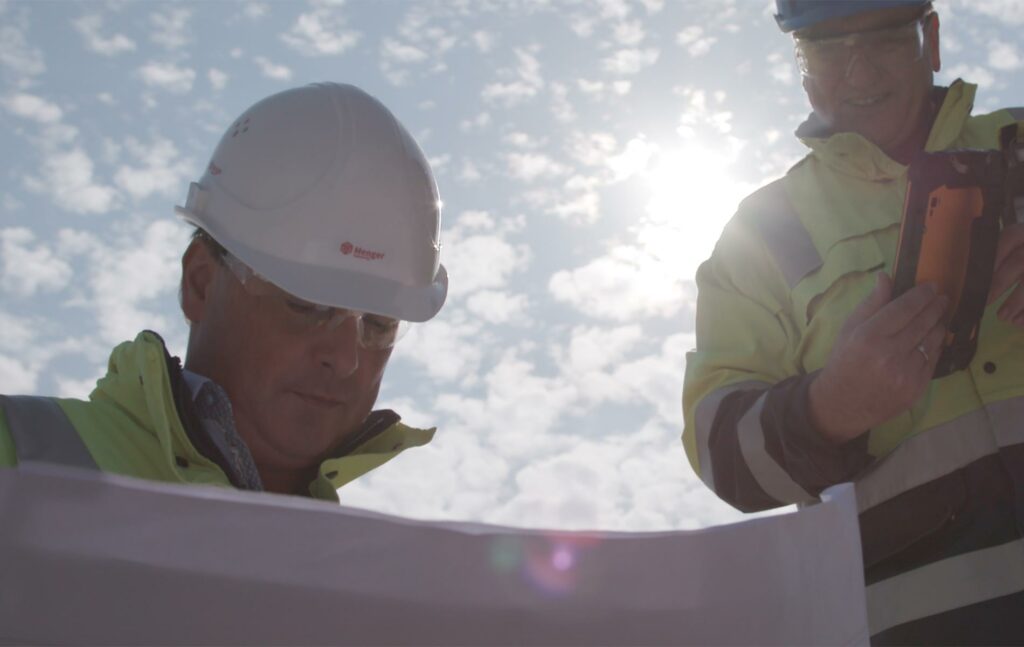