Definition Maintenance: What is it?
Holistic maintenance is necessary for the smooth operation of machines and plants. Read how this is defined at the Menger Group.
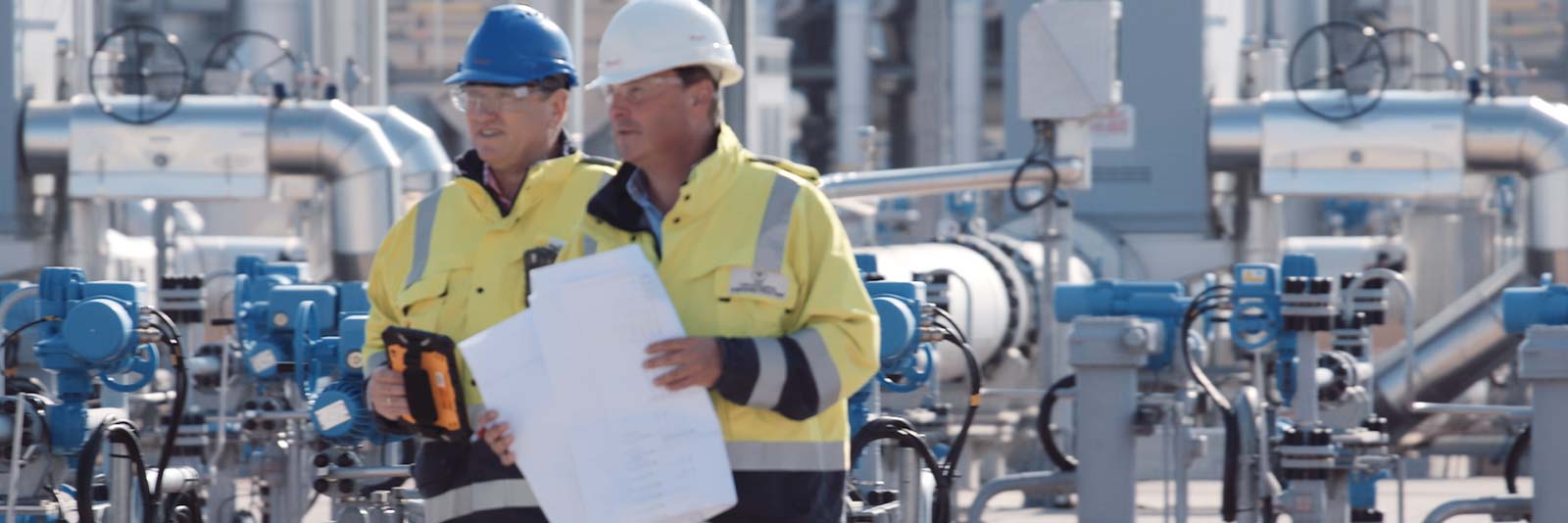
Keeping machines and plants running reliably - maintenance ensures functionality
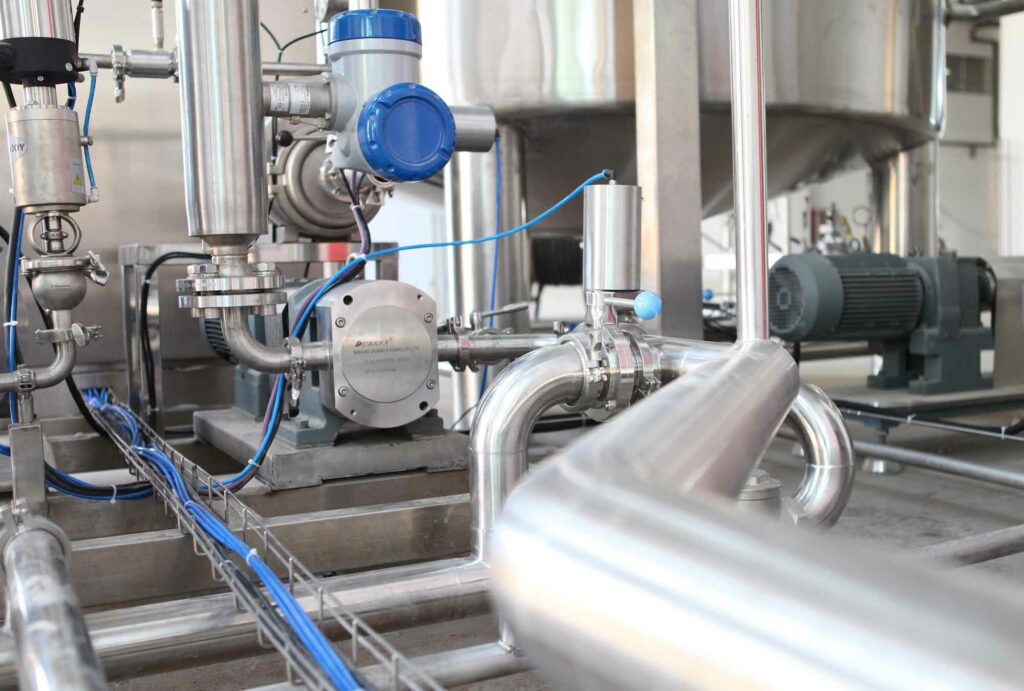
During the life cycle of machines and production plants, maintenance measures are always necessary to prevent damage and malfunctions. Constant competitive pressure, high demands on quality assurance and ensuring that production processes run as smoothly as possible have led many companies to introduce their own maintenance and servicing systems to minimize the risk of plant breakdowns. Professional maintenance involves a combination of administrative and technical measures that ensure the target condition of a machine or system or restore it in the event of a malfunction. In industry, three main maintenance strategies are commonly defined: corrective, preventive and predictive maintenance. The Menger Group explains what these are in detail.
Keeping machines and plants running reliably - maintenance ensures functionality
According to the DIN 31051 and DIN EN 13306 standards, maintenance comprises a range of technical and administrative measures as well as management measures that are intended to ensure the preservation of technical objects or restore their functionality. According to the definition of DIN 31051, maintenance includes four basic measures: Inspection, maintenance, repair and improvement.
- An inspection is defined as a measure to determine the actual condition of a machine or system. This is carried out as part of a function check, which compares the measured values determined with the specified target values.
- By definition, maintenance serves to maintain the target condition. It includes cleaning work, checking settings, and making components fit for use. (The occasional use of the term “maintenance” as a synonym for “servicing”, on the other hand, is incorrect; it is probably based on an incorrect translation of the English word “maintenance”, which encompasses both meanings).
- A maintenance or repair serves to eliminate damage or signs of wear, which can result in a hazard or an imminent functional failure of the system.
- Finally, an improvement measure is a measure to increase functional safety without changing the function of the object.
The forms of maintenance: an explanation
Comprehensive, standard-compliant maintenance is one of the basic prerequisites for ensuring the reliable productivity of a plant. There are three main types of maintenance: corrective maintenance, preventive maintenance and predictive maintenance.
- Corrective maintenance is performed when damage has occurred. This can be done either immediately or postponed, e.g. at the next scheduled maintenance.
- Preventive maintenance is performed before machine or system failures occur. The aim is to minimize the probability of failure. When preventive maintenance is scheduled, the history of the object must be taken into account, as this contains important information on required spare parts, necessary releases and last changes. Digital document management is therefore also becoming increasingly important in maintenance.
In preventive maintenance, a further distinction is made between predefined and condition-based measures. The predefined maintenance measures include contractually agreed maintenance at fixed dates. Condition-oriented maintenance measures, on the other hand, are defined as requiring regular checks of the actual condition, efficiency and other indicators. This involves reading meters, checking measured values, checking the wear of components, etc. This reduces the cost of maintenance because only tasks that are actually necessary are carried out.
- Predictive maintenance is still a relatively new field. This is based on large volumes of recorded, stored and analyzed electronic data. Programs calculate the expected wear and tear and the associated maintenance requirements of components, machines and systems on the basis of certain failure mechanisms and mean time to failure (MTTF) statistics. Predictive maintenance forms an important component in Industry 4.0 and will continue to gain in importance in the future.
If you need professional support in maintenance, you will find a reliable and competent partner in the Menger Group. We offer you well thought-out services and software solutions for all aspects of electronic plant documentation and document management. Contact us!